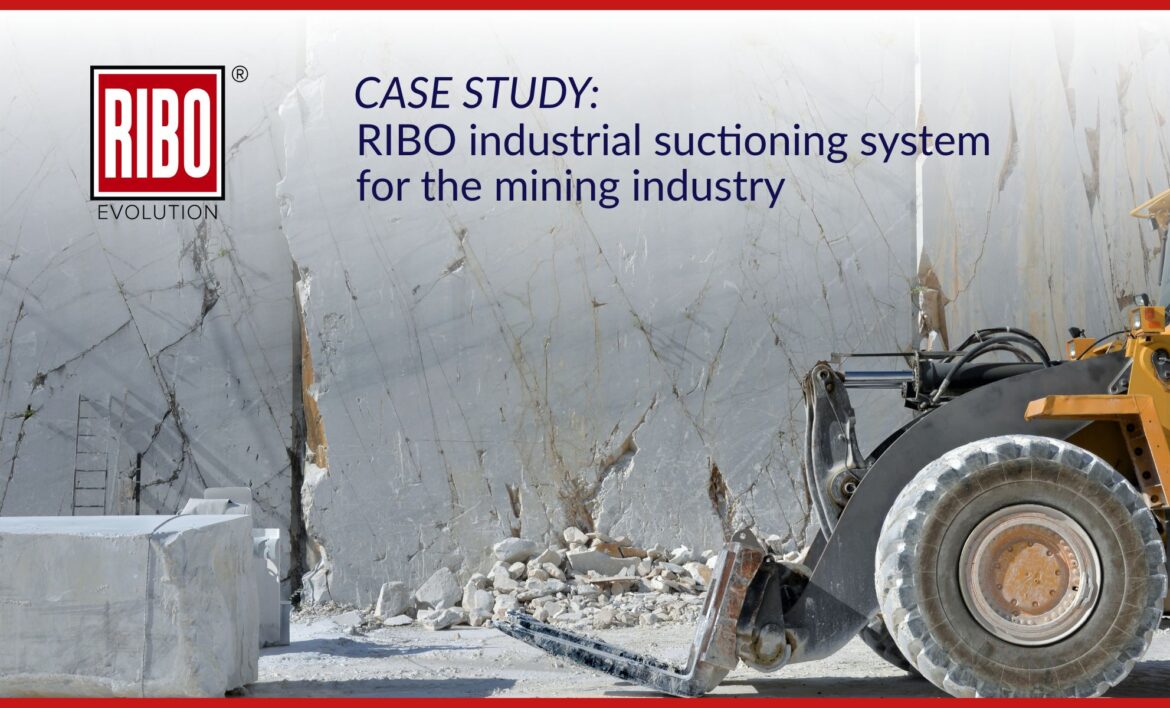
Today we take you with us in the heart of Veneto, in the province of Vicenza, where a historical company in the mining and extractive sector has been operating for more than 170 years. For them, we have studied an ad hoc industrial suctioning system.
The company’s needs
Leader in the production and sale of stone, marble and granite products for floors, stairs and coverings, the Vicenza-based company contacted us to optimize the production process by designing an industrial suctioning system that would overcome their difficulties.
When working in quarries to extract stony materials, it is essential to first make the working environment safe. In fact, during the cutting process of these fine materials, a lot of waste is produced, such as stones, sands and fine dust, which can be harmful to the health of the operators. Since this is a closed environment with almost no air circulation, it is important to free the work area from any processing residue, ensuring clean and healthy air.
Another primary need in the mining sector is certainly that of transporting waste material to clear the work area. In particular, the Vicenza-based company needed to transport wet sandy material produced during stone block cutting operations. By automating this process, operators can work more easily, without having to worry about collecting and moving the waste material manually.
Last but not least, it was necessary to design a practical and manageable industrial suctioning system. As a matter of fact, working in underground quarries characterized by irregular pavement, it was necessary to study a custom-made system that would allow to remedy remarkable differences in height of the ground and that could be easily transported during the cutting operations.
One vacuum cleaner for many needs
Having listened carefully to the customer’s needs, RIBO technicians set to work to study a system that would meet the needs highlighted by the customer. In order to design the best solution for them, our R&D engineers requested a sample of material directly from the quarry to perform specific tests. These tests are of primary importance to estimate the correct power of the industrial suctioning system and to simulate material loading/unloading performance, thus identifying the correct hopper size and the most suitable unloading system for the customer’s needs.
Once the measurements were made, our technicians designed a customized industrial suctioning system, consisting of a vacuum cleaner connected to a hopper with continuous big bag unloading system through a rotary valve system. In other words, the suctioned material is collected by the hopper, which releases it continuously into the collection container. This system avoids clogging and possible machine stops due to material release.
Having to transport heavy materials, RIBO’s experts then reinforced the structure of the vacuum cleaner by installing eyebolts to allow operators to lift the entire system by crane and position it in the exact spot where material suction is required.
To overcome the problem of transporting the system, our technicians provided the vacuum cleaner with sturdy and stable wheels, equipped with brakes, in order to move it easily on uneven ground. Moreover, they studied a special structure that allows the adjustment and modulation of the vacuum cleaner legs on uneven floors.
“We couldn’t have asked for better,” says the Extraction Manager. “Thanks to the RIBO system, we were able to optimize our extraction processes, making the workflow smoother and minimizing downtime. In addition, thanks to our new industrial suctioning system, we are sure to work in healthier and cleaner environments, where there are no environmental risks to our health”.