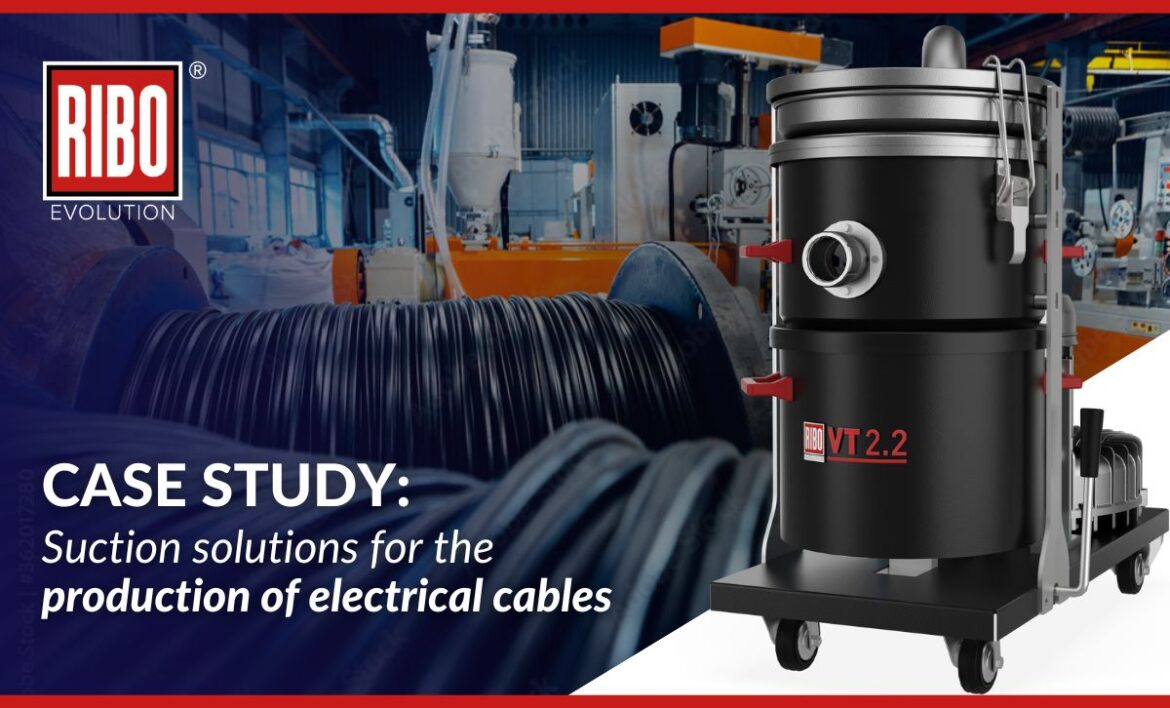
The production of electrical cables is a highly specialized process that requires advanced technologies, not only to ensure high production efficiency but also to maintain high standards of quality and safety. One of the key needs in this process is the effective suction of waste and dust, particularly during the talc application phase. This operation involves the removal of talc residues and other insulating materials that could compromise the quality of the product or damage the equipment. In this article, we will analyze the most suitable suction solutions to meet these needs, with a focus on RIBO industrial vacuum cleaners and their integration into the production process.
Types of waste generated in the production of electrical cables
During the production of electrical cables, various types of waste and residues are generated, which must be managed efficiently. The main waste materials include:
- Fine dust from insulating materials, such as PVC, PE, and other plastic compounds, used to coat the conductors.
- Talc residues, which are applied during the cable coating process.
- Fragments of metal or plastic, resulting from the cutting and processing of conductors and insulators.
These waste materials can affect the quality of the finished product and production efficiency, making a reliable and powerful suction system essential.
The talc application process in cable production
Talc application on electrical cables is a crucial step in the production process. During cable coating, a thin layer of talc, a very fine mineral powder with lubricating properties, is applied for several purposes:
- Facilitating installation: Talc reduces friction between cables and conduits, making them easier to pull through during installation.
- Preventing adhesion: Talc prevents cables from sticking to each other or other materials, especially during storage and transport.
- Protecting the coating: Talc preserves the integrity of the cable’s insulating coating, reducing the risk of damage or abrasion.
This process is particularly common in the production of electrical cables, telecommunications cables, and fiber optic cables. The RIBO VT2.2 159 vacuum cleaner is an ideal solution for vacuuming excess talc, keeping the process clean and efficient.
Suction needs in the talc application phase
An essential aspect of the electrical cable production process is talc application, an operation that involves applying a thin layer of talc to the cables. This talc serves several functions, including reducing friction during installation, preventing cables from sticking together, and protecting the insulating coating from abrasions and damage. However, talc can easily disperse into the production environment, requiring an efficient suction system to avoid dust accumulation.
An effective suction system must meet several needs:
- Immediate removal of excess talc to prevent it from settling on the cables or equipment.
- Maintenance of a clean and safe working environment, minimizing the risk of contamination.
- Adaptation to the production line, with targeted suction at the points where the most residues are generated, such as near the talc application nozzles.
VT line vacuum cleaners for cable production
The RIBO VT line is specifically designed to tackle the challenges associated with managing fine dust and solid materials in production environments. These devices stand out for their robustness and versatility, making them perfect for handling residues like talc used during cable production.
The VT2.2 159 vacuum cleaner, in particular, has been developed to integrate seamlessly into production lines where talc is applied, ensuring a clean and efficient production process. With its ability to vacuum fine dust and solid materials without interfering with production, this model ensures a safe work environment and protects the quality of cable coatings from being compromised.