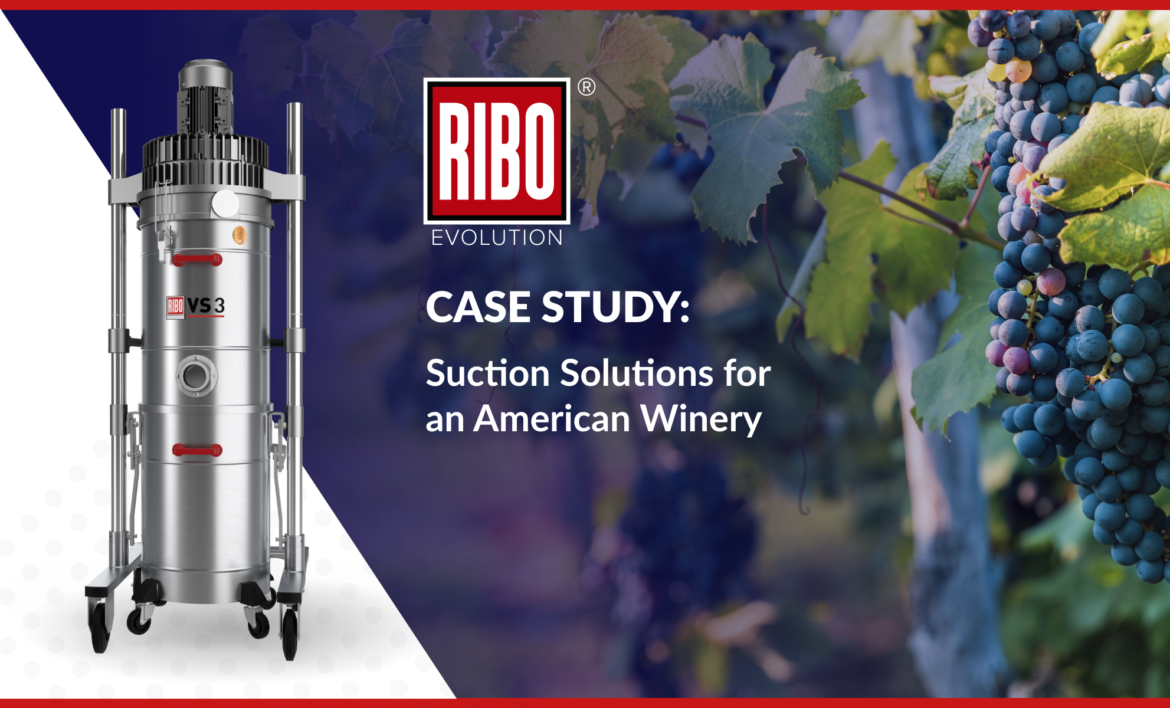
In the fascinating landscape of the wine industry, optimizing operations plays a crucial role in ensuring the production of excellent quality wines. Through the analysis of this case study, we will explore how a collaborative approach and a strategic partnership contributed significantly to the operational success of an American winery. We will highlight how RIBO, a company specialized in industrial vacuuming, has led to a significant improvement in the wine production process.
A strategic collaboration between RIBO and the wine company
The collaboration undertaken between RIBO and the American wine company has resulted in a number of significant benefits. The starting point was a detailed analysis of the winery’s aspirational needs. Then, once the challenges were identified, RIBO provided the professionalism of its team by offering the most suitable vacuum solution.
Identifying challenges
By carefully examining the path of the American winery, several areas of interest emerged that led to the analysis of targeted suction solutions.
Below are the key points taken into consideration:
- Particle removal:
One of the main challenges faced concerns the effective removal of suspended particles during processing. Residual dust and foreign substances, inevitably present in the production environment, can have a negative impact on the taste and purity of wines, as well as affecting the efficiency of equipment.
- Safety and hygiene:
Attention to safety and hygiene is crucial for the winery. The accumulation of particles in the air compromises the working environment for operators, and can also compromise the quality of the wines. An inadequate working environment could threaten the reputation of the company and the integrity of the products themselves.
- Energy efficiency:
The company carefully faces the aspect of vacuum cleaning, seeking to balance the demand for optimal performance with responsibility towards the environment and energy efficiency. The company has demonstrated a willingness to adopt sustainable solutions by exploring advanced and innovative vacuum cleaner systems, including our industrial vacuum cleaners, which are at the forefront of balancing performance and sustainability. Moreover, among the distinguishing features of RIBO’s vacuum cleaners we find the construction of the vacuum cleaners themselves, which are structurally made without plastic.
Suction solution design and implementation
The design and customization of vacuum solutions were the key element of this successful partnership between RIBO and the American winery. This critical phase saw the transition from theoretical concepts to practical solutions, facing the challenges identified during the initial analysis.
The RIBO design team realized innovative, tailor-made solutions, which then led to tangible changes within the winery, improving and optimizing the wine production process. Furthermore, the integration of the industrial vacuum system took place without causing disruption to the winery’s existing workflow, thus minimizing operational impact.
Benefits for the winery that implemented the industrial vacuum system
The winery that choose to implement the industrial vacuum system enjoyed a number of benefits that helped to improve several aspects of its operations:
- Product quality
The reduction of suspended particles in the production environment has led to a significant improvement in the quality of the final product. Wines have become purer and free of contaminants offering a superior sensory experience to consumers;
- Healthy working environment
The reduction of airborne particles has created a healthier and more comfortable working environment for operators. This has helped to improve operator satisfaction and safeguard their health.
- Reducing waste
An efficient industrial vacuum system captures and removes excess or unwanted materials during the production process. This leads to a reduction in raw material waste and optimizes resource utilization.
The three-phase RIBO industrial vacuum cleaners of the VS line are specifically designed for use in working conditions that require robustness, practicality and low noise levels. They are able to withstand intensive 24/7 use, maintaining an exceptionally long-life cycle and ensuring high performance and reliability at the highest level.
They can be used for cleaning after production phase as well as during production phase. All models are also available in stainless steel, ideal for the food industry, where it is required maximum hygiene and sterilization of working machinery.