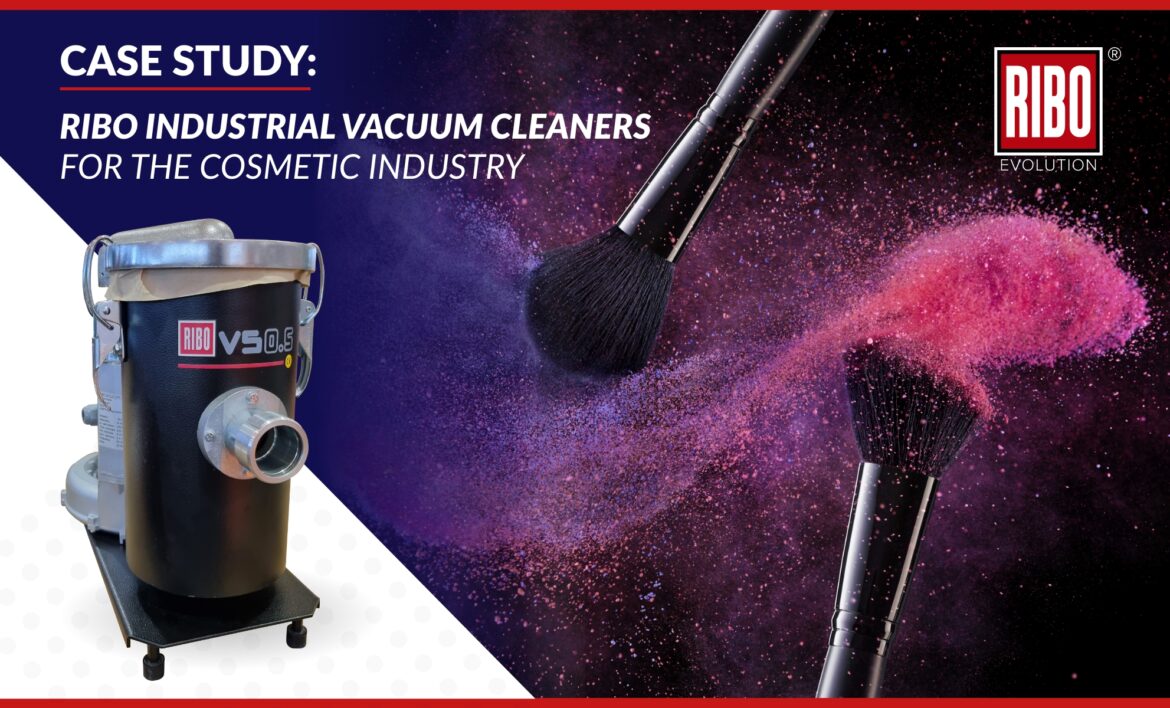
The cosmetic industry deals with the production and marketing of products designed to improve the appearance and health of the skin, hair and body in general. It is an industry that embraces the production of a wide variety of products, such as creams, shampoos, conditioners, make-up, perfumes and nail products.
In this case study, we will discuss what are the types of waste produced by the cosmetic industry, the risks involved, the suction needs and the advantages of using an industrial vacuum cleaner. At the end, we will find out the features of the RIBO vacuum cleaner chosen by one of our clients, engaged in this industry.
You will find:
- What are the wastes produced by the cosmetic industry
- The needs of the company
- The advantages of RIBO’s vacuum cleaner in the cosmetics industry
- RIBO vacuum cleaner line for the cosmetic industry: VS 0.5
What are the wastes produced by the cosmetic industry
Different types of waste can be generated at different stages of the production process. We want to focus our attention on the waste that is created during the production and packaging stage of the product. At these stages, the waste that is generated can be mainly: chemical waste in liquid or powder form, or waste materials from packaging.
– Chemical waste
In the cosmetic industry, the operator is constantly handling chemicals, different from each other, which can cause damage in an immediate way on the health of human beings; or, when exposure persists incorrectly and prolonged, the damage can become chronic.
The inhalation of these chemical fumes and dusts, must be prevented through special safety devices worn by the operator, or through special industrial vacuum systems installed on the specific areas.
In addition to the damage that chemical waste can cause on human health, it can also provoke problems to the success of the final product. In fact, if not handled and collected properly, they can lead to contamination between one product and another, altering the properties of the individual product and causing its failure.
– Packaging waste
During the packaging stage are produced scraps related to the cutting or closing of packages; they can be micro particles of different materials that need to be collected for proper disposal.
The needs of the company
Our client produces a large quantity in free and compact form of powders and liquids generated by mixing different raw materials, which are then transformed into powders, blushes, eye shadows mixed with various pigments. The different stages of processing are carried out by to specific machinery controlled by the operators, it is on this machinery that our client needs to integrate industrial vacuum cleaners. The final goal is to keep the work area clean and prevent the operator from coming into contact with harmful substances.
The advantages of RIBO’s vacuum cleaner in the cosmetics industry
The suction solutions offered by RIBO make it possible to fulfill the needs of the company engaged in the production of cosmetics. Thanks to the installation of our industrial vacuum cleaners, the advantages from which the company can benefit are as follows:
- Professional air purification
- The maintenance of a high standard of cleanliness of the working environment
- The prevention of damage to operators’health
- Avoiding contamination between different batches, ensuring a high quality end product
RIBO vacuum cleaner line for the cosmetics industry: VS 0.5
The line of industrial vacuum cleaners offered by RIBO for the cosmetic industry enables the proper suction and filtration of dusty and liquid materials generated during production processes.
The VS 0.5 line of vacuum cleaners features a 0.5 kW three-phase multi-voltage motor and is specially designed to work in a continuous cycle, in compliance with the latest current regulations on energy saving. It is available in different configurations depending on customer requirements, for example, it can be configured in compact or modular mode.
Container capacities range from 1.2 liters up to 8 liters, and it is possible to include HEPA/ULPA absolute filters -which allow the most toxic and harmful components to be filtered out- and activated carbon filters in blow molding.