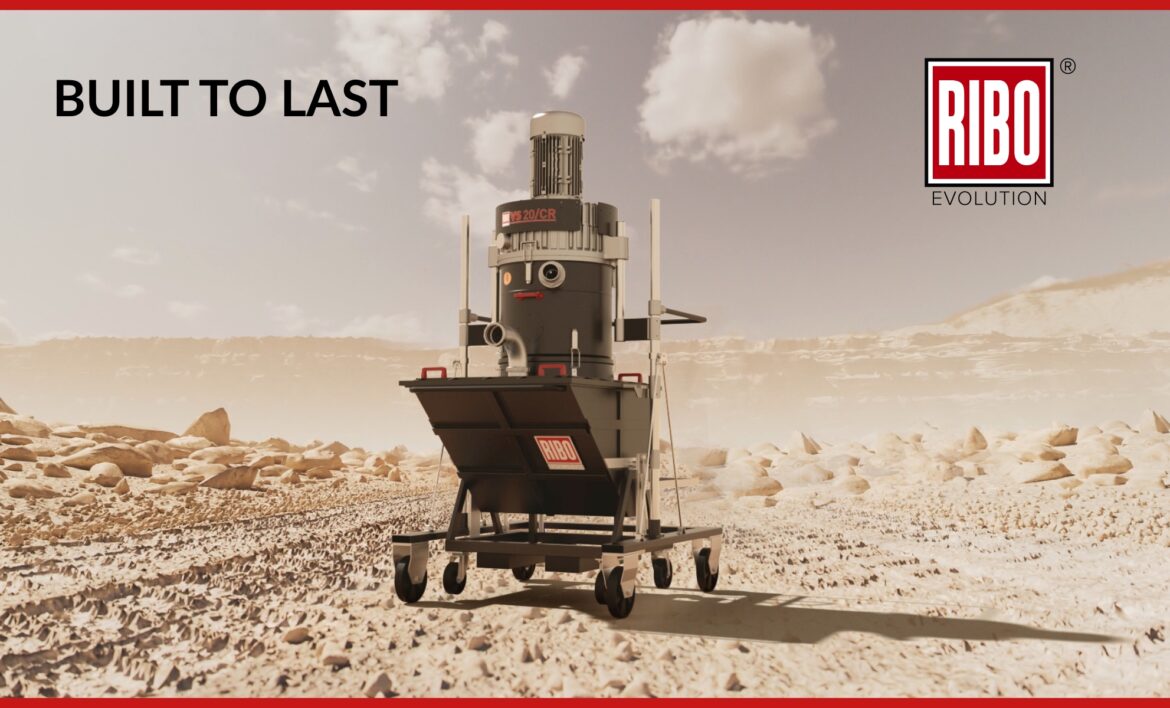
RIBO’s recipe for success is one: the structural robustness of our industrial vacuum cleaners. Companies looking for a robust and durable vacuum cleaner know that they can find these features in RIBO. In more than 50 years of business, we have built and provided thousands of companies with industrial vacuum cleaners that are unique in terms of performance and product quality, today we are still carrying out our mission.
In this article we will argue some technical aspects according to which we can proudly say that RIBO vacuum cleaners are built to last.
What makes a RIBO vacuum cleaner indestructible?
Proceeding in order, we are going to examine several parts that make up a RIBO vacuum cleaner to better understand what materials are used and the features that make it structurally robust.
Suction unit
The suction unit is managed independently by our RIBO experts and is made on our own molds. Not any detail is left to chance; we maintain total control of the production process. Then, we make some fluid dynamic studies of the profile of the fins, in order to optimize the speed triangles.
Motor
The motors of RIBO vacuum cleaners are rigorously selected and are among the most reliable on the market. They are composed of extremely solid and durable materials: steel and aluminum alloy, with the total absence of plastic. This choice is made for two reasons:
- To ensure reliability, strength and high performance over time, minimizing maintenance work, even after years of use;
- For an environmental sensitivity that distinguishes us, to which we pay close attention, both in the construction and in the disposal of our vacuum cleaners, thanks to our scrapping service.
Calendered sheet metal
We use 12/10 millimeter sheets to make the parts of the machine where vacuum is generated extremely strong. This solution allows us to optimize the performance of the vacuum cleaner and guarantee the efficiency of the vacuum cleaner over time. In this way, it is best preserved from damage due to wear, shock, or improper use.
Support elements
Support elements are made from steel and aluminum alloy. Their structure is oversized and made from proprietary molds. This promotes total control of the production process and exceptional strength and mechanical resistance. RIBO vacuum cleaners are capable of withstanding extremely heavy workloads, even in the most difficult situations.
Wheels
The wheels is also structural oversized, each wheel could bear the entire weight of the machine. This is a unique feature that enables RIBO vacuum cleaners to easily withstand the most extreme stress, even under the heaviest load conditions. The rolling capacity of the wheels makes it possible to move effortlessly heavy-weight vacuum cleaners.
The acceptance tests of a RIBO vacuum cleaner and the stress test phase
Each RIBO vacuum cleaner is delivered to the customer following a series of acceptance tests. These are divided into three macro tests: electrical testing, functional testing, and performance testing.
Together with our RIBO experts, we delved into what testing checks are carried out for each area:
Electrical testing
In the electrical testing stage, we test the correctness of:
- execution of electrical panel and on-board wiring
- execution grounding of the various parts of the machine (conductive or antistatic parts)
- adjustment of thermal protection devices
- motor starting and switching times
- filter cleaning system
Functional testing
At this stage, all machine functionality is tested as the operation of sensors, actuators and motors.
Performance testing
We check the performance of the machine in terms of developed vacuum and possibly volumetric flow rate.
At the end of the test, a stress test is performed. The machine is subjected to its 100 percent load capacity for a sufficient time to bring to temperature all the under stressed parts. We check machine endurance and the suitability of a list of measurements including: developed temperatures and proper heat dissipation, noise, vibration, and electrical absorption.
RIBO, the vaccum cleaners built to last!