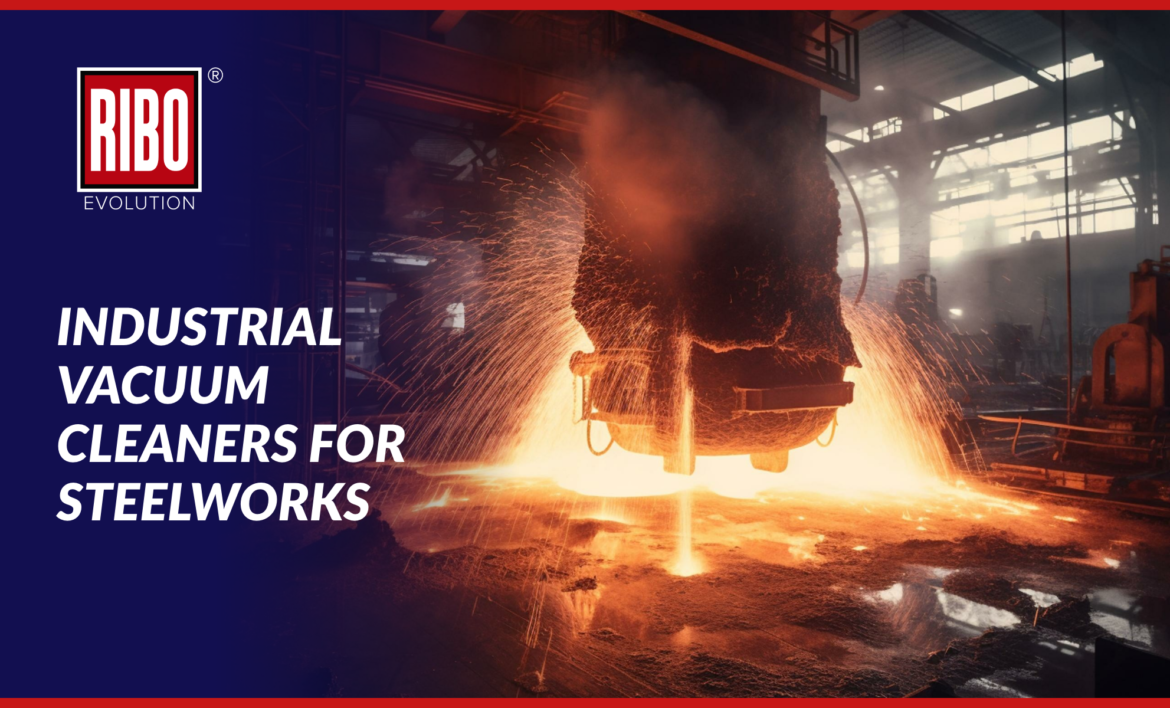
Steelworks play a very important role in the production of steel, an indispensable material for numerous industries nationally and internationally.
During the processing of steel, large amounts of waste are generated, which it becomes essential to properly vacuum to avoid:
- Production slowdowns
- Health hazards to operators
- Unnecessary waste of time that may result from increased maintenance demands
- Imperfections in the manufacture of products
Therefore, it becomes necessary for companies to equip themselves with industrial vacuum systems that are powerful and suitable for removing large amounts of waste effectively, capable of withstanding harsh conditions and intense work pace.
What are the wastes produced by steelworks
Steelworks produce different types of scrap, that change according to the process used and the degree of recycling implemented. Some of the main wastes produced by steelworks include:
- Slags
They result from the melting of ferrous and nonferrous materials and contain the impurities in the raw materials used, including silica, iron oxide, limestone, and magnesia.
- Steel powders
During steel processing, very fine dusts consisting mainly of iron particles and other impurities are generated. These dusts require proper management and disposal, as they can be toxic and polluting if released into the environment.
- Cutting waste and metal scrap
During the steel forming and processing process, cutting waste, shavings and unused metal pieces can be produced. These scraps can be collected and recycled to reduce waste and recover valuable material.
- Calamine
This is a dense substance that forms during the cooling of metal bars and accumulates in the rollers and under the conveyor lines, causing malfunctions and long-term failures.
- Emissions and blast furnace fumes
Some steelmaking processes involve the use of blast furnaces, which emit fumes containing particulate matter and waste gases. Efforts to reduce pollutant emissions and recover energy from these waste gases are often part of steel mills’ efforts toward sustainability.
To meet these needs, RIBO industrial vacuum cleaners play a crucial role, ensuring efficient and safe production.
What are the vacuum needs
The suction requirements of steelworks are different, depending on the stage of steel processing, and concern:
FURNACE CLEANING
The role of the furnace is crucial within the steel production process; it is an essential element for steelworks. The smelting process generates large amounts of waste material, which is often removed manually, thus lengthening furnace downtime and consequently slowing steel production.
Using a proper vacuum cleaner allows you to greatly reduce furnace cleaning time, which also reduces maintenance work.
THE REMOVAL OF PRODUCTION WASTE AND CALAMINE
Calamine is produced during the cooling of metal bars and is a heavy material, which accumulates in large quantities on machines and working tools, causing, in the long run, the malfunction of equipment, also accelerating its wear and tear.
CLEANING THE OVERHEAD CRANE
Dust generated by melting is deposited on the overhead crane, this can cause problems with handling and even electrical circuits, risking stopping the entire production process. The solution to safely and quickly recover the dust that is deposited on the overhead crane is to install a centralized vacuum system.
THE SUCTION OF DUST FROM THE SANDBLASTING PROCESS
Once the blank is retrieved from the furnace, it is polished through the sandblasting process. This processing step takes place inside enclosed booths where a large amount of abrasive material used for sandblasting is collected. It is necessary to remove these harmful sands with appropriate industrial vacuum cleaners
The advantages of RIBO’s vacuum cleaner in steelworks
Adopting an industrial suction solution designed specifically for the needs of steelworks promotes a number of advantages such as:
- Healthy and safe working environment
Steel mills generate dust and pollutants that are hazardous to workers’ health. It is essential to effectively remove these materials to avoid risks of intoxication and respiratory problems.
- Operating cost savings
Without a proper vacuum system, dust cleaning and removal may require more resources and manpower, increasing the company’s overall operating costs.
- Increased productivity
A high-performing vacuum system frees operators from cleaning and material disposal tasks, allowing them to focus on core production activities.
The vacuum solutions offered by RIBO
RIBO offers a wide range of suction solutions designed to meet the needs of the steelworks. VS line vacuum cleaners are capable of sustaining intensive and continuous use even for 24 hours a day, maintaining an exceptionally long-life cycle and ensuring high performance and reliability at the highest level.