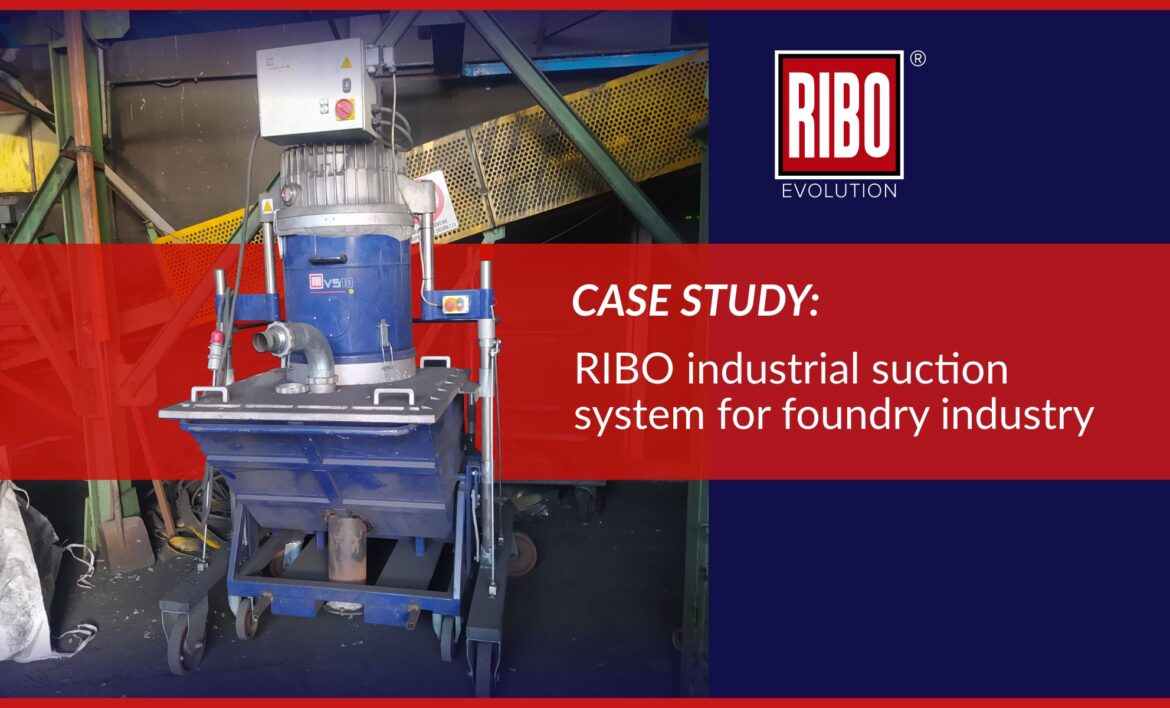
Acording to a recent study by Assofond (Italian Foundry Association), there are more than 1,000 foundries only in Italy, producing a total of about 2.3 million tons of castings. This is a figure that ranks Italy second in Europe, after Germany, and ninth in the world. So we are talking about a very important sector both for the economic impact it produces and for the production of end products that are indispensable for various activities.
In particular, a foundry is concerned with making “castings,” they are industrial or artistic products, with well-defined metallurgical and dimensional characteristics. The process starts with the casting of ferrous and nonferrous metal materials; these are cast in refractory material molds or inside metal molds, then cooled to obtain the desired shape.
The needs of the company
In today’s case study, we will describe the history of a famous italian foundry established about 70 years ago, which produces cast iron components for various industries, it is specializes in the hydraulic, motor, and mechanical component industries.
The problem of this company, which RIBO has solved, is as follows: once the solidified product is removed from the mold, it must undergo a process called “finishing,” for the removal of the core, soil, burrs, and slag from castings that allow the finished product to be obtained.
The finishing process consists of several stages, where the produced component must be transported along the production line producing a large amount of metal dust that is deposited in the work environment, forming large piles od dust that must necessarily be vacuumed at the end of each day or production cycle, to keep the plant running efficiently.
VS 10 499 CR in action
In this well-known foundry, the RIBO vacuum cleaner being used is a VS line model 10 499 CR. It is an industrial vacuum cleaner equipped with a 450-liter container, which enables it to quickly suck up a large amount of metal dust. It often is very heavy, clogging, and volatile, such as cast iron and waste from the other components used for the creation of the end product.
The bucket release and discharge system remains very practical and makes it easier for the operator to empty the container. This becomes a quick operation, which also reduces the time of cleaning of the environment. In this case, we also find an oversizing of the wheeled structure to easily withstand the most extreme stresses, even under the heaviest loading conditions.
Why did the client choose RIBO?
Today’s case study deals with a historical client of RIBO; in fact, the client trusted us more than 40 years ago. Throughout all these years, the customer has always been satisfied with the quality of RIBO’s products, choosing us whenever he needed to upgrade his fleet of vacuum cleaners. Having to endure tight work schedules, the vacuum cleaner features he was looking for were always those offered by RIBO: reliability, structural robustness and excellence.